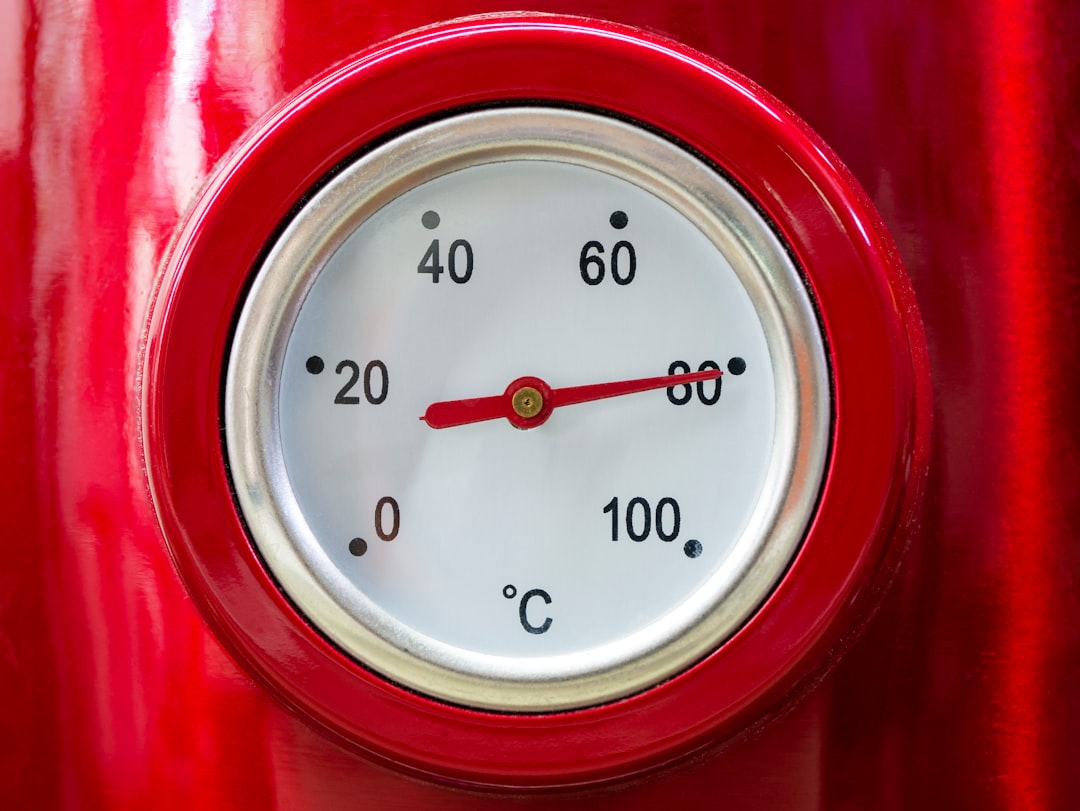
Maximizing Efficiency: The Role of Gas Regulators
Gas regulators are essential components in any gas system, as they control the flow and pressure of the gas being delivered. The primary function of a gas regulator is to reduce the high pressure of the gas in a cylinder or pipeline to a lower, more manageable level for use in various applications. This is crucial because many gas-powered devices and equipment require a specific pressure to operate efficiently and safely. Gas regulators achieve this by using a diaphragm or piston mechanism to balance the force of the incoming high-pressure gas with a spring-loaded mechanism, which then delivers a consistent and controlled flow of gas at the desired pressure.
Gas regulators are commonly used in a wide range of industries, including manufacturing, healthcare, laboratories, and residential settings. In manufacturing, gas regulators are used to control the flow of gases such as oxygen, nitrogen, and argon for welding, cutting, and other industrial processes. In healthcare, gas regulators are crucial for delivering medical gases such as oxygen and nitrous oxide to patients in hospitals and clinics. In laboratories, gas regulators are used to control the flow of specialty gases for research and analysis. In residential settings, gas regulators are used for household appliances such as stoves, water heaters, and grills. Understanding the function of gas regulators is essential for selecting the right regulator for a specific application and ensuring its proper installation and maintenance.
Gas regulators play a critical role in ensuring the safe and efficient delivery of gas for various applications. By understanding their function, users can make informed decisions about selecting the right regulator for their specific needs and ensure its proper installation and maintenance for optimal performance.
Key Takeaways
- Gas regulators control the flow and pressure of gas in a system to ensure safe and efficient operation.
- Selecting the right gas regulator involves considering factors such as gas type, flow rate, and inlet pressure.
- Proper installation and maintenance of gas regulators is crucial for ensuring their effectiveness and longevity.
- Pressure control is essential for maximizing efficiency and preventing damage to equipment in gas systems.
- Gas regulators enhance safety and reliability by preventing overpressure and ensuring consistent gas flow.
Selecting the Right Gas Regulator for Your Application
Selecting the right gas regulator for a specific application is crucial for ensuring safe and efficient operation. There are several factors to consider when choosing a gas regulator, including the type of gas being used, the required flow rate and pressure, the environmental conditions, and any specific industry standards or regulations that need to be met. Different gases have different properties and requirements, so it’s essential to select a regulator that is compatible with the specific gas being used. For example, some gases may require special materials or seals to prevent corrosion or contamination.
The required flow rate and pressure also play a significant role in selecting the right gas regulator. Different applications may require different flow rates and pressure levels, so it’s essential to choose a regulator that can deliver the required performance. Environmental conditions such as temperature, humidity, and altitude can also impact the performance of a gas regulator, so it’s important to consider these factors when making a selection. Additionally, certain industries may have specific standards or regulations that need to be met, so it’s crucial to choose a regulator that complies with these requirements.
In addition to these factors, it’s also important to consider the quality and reliability of the gas regulator. Choosing a reputable manufacturer with a proven track record of producing high-quality regulators can help ensure that the regulator will perform as expected and have a long service life. By carefully considering these factors, users can select the right gas regulator for their specific application and ensure safe and efficient operation.
Proper Installation and Maintenance of Gas Regulators
Proper installation and maintenance of gas regulators are essential for ensuring their safe and efficient operation. When installing a gas regulator, it’s crucial to follow the manufacturer’s instructions and any applicable industry standards or regulations. This includes ensuring that the regulator is installed in the correct orientation, with the inlet and outlet connections properly aligned, and any necessary support or mounting brackets are used. It’s also important to ensure that the regulator is installed in a location that is easily accessible for maintenance and inspection.
Regular maintenance is also critical for ensuring the continued performance of a gas regulator. This includes inspecting the regulator for any signs of damage or wear, checking for leaks or other issues, and replacing any worn or damaged components as needed. It’s also important to periodically test the performance of the regulator to ensure that it is delivering the required flow rate and pressure. This can be done using a calibrated pressure gauge or flow meter to compare the actual performance of the regulator with its specified performance.
In addition to regular maintenance, it’s also important to address any issues or malfunctions promptly. If a gas regulator is not performing as expected or if there are any signs of damage or wear, it should be taken out of service and inspected by a qualified technician. This can help prevent potential safety hazards and ensure that the regulator continues to operate safely and efficiently.
By following proper installation and maintenance procedures, users can ensure that their gas regulators operate safely and efficiently throughout their service life. This can help prevent potential safety hazards and ensure that the regulator continues to deliver the required flow rate and pressure for its specific application.
Importance of Pressure Control in Maximizing Efficiency
Pressure Control Benefits | Explanation |
---|---|
Energy Efficiency | Proper pressure control can reduce energy consumption and improve overall efficiency. |
Equipment Longevity | Maintaining optimal pressure levels can extend the lifespan of machinery and equipment. |
Product Quality | Consistent pressure control can ensure better product quality and reduce defects. |
Safety | Proper pressure control is essential for maintaining a safe working environment and preventing accidents. |
Pressure control is crucial for maximizing the efficiency of gas-powered equipment and processes. Many gas-powered devices and equipment require a specific pressure to operate efficiently and safely. For example, in welding applications, precise control of the gas pressure is essential for achieving high-quality welds with minimal defects. In healthcare settings, accurate pressure control is critical for delivering medical gases such as oxygen and nitrous oxide to patients at the correct flow rate and pressure. In industrial processes, maintaining consistent pressure levels is essential for ensuring product quality and process efficiency.
Proper pressure control can also help reduce energy consumption and operating costs. By delivering gas at the optimal pressure for a specific application, gas regulators can help minimize waste and improve overall system efficiency. This can result in cost savings and environmental benefits by reducing energy consumption and greenhouse gas emissions.
In addition to these benefits, proper pressure control can also help extend the service life of equipment and reduce maintenance requirements. By delivering gas at the correct pressure, gas regulators can help prevent damage to sensitive components and reduce wear on equipment. This can result in longer service life and reduced maintenance costs over time.
By understanding the importance of pressure control, users can make informed decisions about selecting the right gas regulator for their specific application and ensure its proper installation and maintenance for optimal performance.
Enhancing Safety and Reliability with Gas Regulators
Gas regulators play a critical role in enhancing safety and reliability in gas systems. By controlling the flow and pressure of gas, regulators help prevent over-pressurization of equipment and pipelines, which can lead to safety hazards such as leaks, fires, or explosions. Gas regulators also help ensure that gas-powered devices and equipment operate within safe pressure limits, reducing the risk of malfunctions or accidents.
In addition to safety benefits, gas regulators also contribute to system reliability by delivering consistent and controlled flow of gas at the desired pressure. This helps ensure that equipment operates as intended, reducing downtime and improving overall system performance. By maintaining consistent pressure levels, gas regulators also help prevent fluctuations in gas flow that can impact product quality or process efficiency.
Gas regulators are designed with safety features such as relief valves or built-in pressure gauges to provide additional protection against over-pressurization or other potential hazards. These features help ensure that gas regulators operate safely under normal operating conditions as well as in the event of unexpected events such as pressure surges or equipment malfunctions.
By enhancing safety and reliability in gas systems, regulators help protect personnel, equipment, and facilities from potential hazards while ensuring consistent performance and efficiency. This makes them essential components in a wide range of industries where gas is used for various applications.
Optimizing Performance with Advanced Gas Regulator Technology
Advanced gas regulator technology offers several benefits for optimizing performance in gas systems. One key advancement is the development of precision regulators that provide more accurate control of gas flow and pressure. These regulators use advanced materials and design features to deliver precise performance over a wide range of operating conditions, making them suitable for a variety of applications.
Another advancement is the integration of electronic controls into gas regulators, allowing for more precise monitoring and adjustment of pressure levels. Electronic regulators can provide real-time data on system performance, allowing operators to make informed decisions about system operation and maintenance. They can also be integrated into automated control systems for enhanced efficiency and reliability.
Advanced materials such as corrosion-resistant alloys or polymers are also being used in modern gas regulators to improve durability and performance in harsh operating environments. These materials help extend service life and reduce maintenance requirements, resulting in cost savings over time.
In addition to these advancements, modern gas regulators are also designed with improved safety features such as redundant pressure relief valves or fail-safe mechanisms to provide additional protection against over-pressurization or other potential hazards.
By leveraging advanced gas regulator technology, users can optimize performance in their gas systems by achieving more precise control of gas flow and pressure, improving system monitoring and automation capabilities, enhancing durability and reliability, and ensuring safety under all operating conditions.
Integrating Gas Regulators into a Comprehensive Efficiency Strategy
Integrating gas regulators into a comprehensive efficiency strategy can help maximize performance while minimizing energy consumption and operating costs. By selecting high-efficiency regulators that deliver precise control of gas flow and pressure, users can optimize system performance while reducing waste and improving overall efficiency.
In addition to selecting high-efficiency regulators, users can also implement advanced monitoring and control systems to optimize system operation based on real-time data on gas flow rates, pressures, and other relevant parameters. This can help identify opportunities for further optimization while ensuring safe and reliable operation.
Proper installation and maintenance practices are also essential components of a comprehensive efficiency strategy for gas regulators. By following best practices for installation and maintenance, users can ensure that regulators operate at peak efficiency throughout their service life while minimizing downtime and maintenance costs.
Furthermore, integrating gas regulators into an overall efficiency strategy can help identify opportunities for system improvements such as equipment upgrades or process optimization that can further enhance overall efficiency while reducing operating costs.
By integrating gas regulators into a comprehensive efficiency strategy that includes high-efficiency equipment selection, advanced monitoring and control systems, proper installation and maintenance practices, and ongoing system improvements, users can achieve maximum performance while minimizing energy consumption and operating costs across a wide range of applications.
If you’re interested in learning more about gas regulators, you should check out this article on legendsnack.com. They have a comprehensive guide on how gas regulators work and the different types available for various applications. It’s a great resource for anyone looking to understand the importance of gas regulators in different industries.
FAQs
What is a gas regulator?
A gas regulator is a device used to control the pressure and flow of gas from a high-pressure source, such as a gas cylinder, to a lower pressure level suitable for use in various applications.
How does a gas regulator work?
A gas regulator works by reducing the high pressure of the gas from the source to a lower, more manageable pressure for use in appliances or equipment. It typically consists of a diaphragm, a spring, and a valve that work together to maintain a consistent outlet pressure.
What are the different types of gas regulators?
There are various types of gas regulators, including single-stage regulators, dual-stage regulators, high-pressure regulators, and low-pressure regulators. Each type is designed for specific applications and pressure requirements.
What are the common uses of gas regulators?
Gas regulators are commonly used in residential, commercial, and industrial settings to control the flow and pressure of gases for heating, cooking, welding, medical equipment, and various other applications.
How do you maintain a gas regulator?
To maintain a gas regulator, it is important to regularly inspect for any signs of damage or wear, ensure proper installation and connections, and follow the manufacturer’s guidelines for servicing and replacement of parts. Regular testing and calibration may also be necessary to ensure proper functioning.